Here's the first of what I hope will be many posts about modifications to my new car, a Hyundai Veloster. I have a long list of ideas for things I want to do with the car and I thought this one was a good starting point. The car has a little tray under the dash directly in front of the shifter where I usually keep my work badge and other small things. I thought it would be a nice addition to have some lights illuminate the tray, but they would have to turn on and off automatically so they're not distracting while driving at night. There are some plastic handle-type things on either side of it, so I planned to put a beam break sensor across those to trigger the lights when someone reaches in.
Here's a schematic for the circuit I designed. It's run by a PIC12F615 and has an IR led and phototransistor for the beam, a 5V regulator, and three white LEDs driven by a MOSFET. After getting the dash open I discovered a good way to include a programming connector so that's included as well.
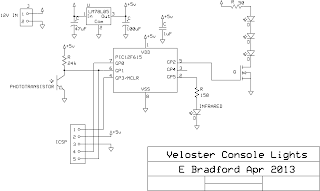
The software for the microcontroller operates the beam break sensor entirely in interrupts, and the main loop interprets that information and loads brightness levels into the PWM peripheral. The algorithm for the beam detection is a technique I've used before (in
Tiny Tank Bot, among other things): the infrared LED is toggled on and off, and I take an analog measurement from the phototransistor in each state. The two values are then compared to see if they differ significantly, which indicates that the IR light from the LED is "visible" to the phototransistor. This technique works well to reject varying levels of visible light (and other sources of IR) that influence the reading from the phototransistor. Repeated comparison results are then accumulated in a counter so that a confirmed detection of the beam requires a number of consistent positive results. The duty cycle of the IR LED is kept low to save power.
The brightness levels for the white LEDs are taken from a logarithmic table, and I played around with a variable timing technique on the ramp up and down until it looked smooth. I have the LEDs stay on at 1% while no objects are detected so there will be a nice glow on the tray. The software ramps up the brightness to maximum as soon as the beam is broken, but it waits for the beam to come back for 1.5 seconds without interruption before dimming back down. This makes the lights stay up for as long as you're reaching into the tray, and then smoothly go back down when you're done. Here's a software test on the breadboard:
Once the software and circuit were proven out, I built the circuit on perfboard. I left the IR LED and sensor on headers so I could disconnect them to make installation easier.
Here's a test of the completed circuit:
Next step was the scary part: disassembling my dash. Luckily I found some instructions from a Hyundai service manual posted on a forum. The center piece of the dash that holds climate controls and two vents is held in by friction clips and can be pried off with plastic tools ( I made some from lexan stock I had on hand).
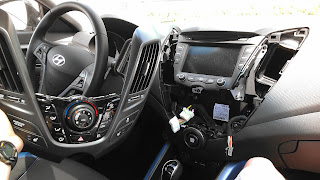
With that piece off there's plenty of room to work in there, and you can see straight down to the piece above the tray (which has the 12V outlets, aux input, and USB port). I could then see how to get that piece off: it's held in by the same type of friction clips, and it just slides straight out towards the shifter. There is a slot to put a (very short) flathead screwdriver in the back to pry it off. If anyone wants to reproduce this, you don't have to take off the climate control piece, just slide that little pod straight out until the clips pop off. I took that piece in to my workbench and prepared an LED board with three cool white XP-Gs. I drilled holes for the LEDs in the plastic and stuck the LED board down with VHB tape.
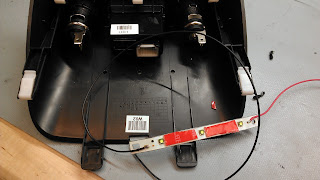
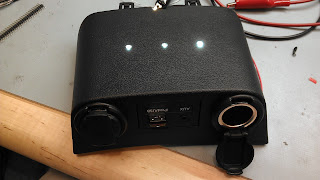
The rest of the circuit went in next. It steals power from one of the 12V outlets, which means this is only active while the car is on. This is not ideal--it would be nice to have it on when you first get in the car and for a short time after turning it off, but this way I can be sure I don't make a mistake that kills the battery while it's parked. I could connect it to a 12V line that's on all the time as it only draws 2-3mA in the idle state, but I didn't want to run new wires to this area.
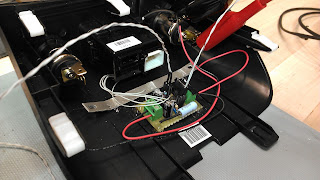
At this point I noticed that the 12V outlets have little cutouts in the metal cylinder that are just big enough to pass a 0.1 header (pin strip) through, which gave me a perfect way to include a programming connector. I wired in the connector and insulated it with electrical tape. I then close the lid on the 12V outlet and it's completely hidden, but I still have the opportunity to update the code if I think of a change I want or if my parameters don't work anymore in the real application. Also, the signal from the phototransistor is shared with the data line, which may help in debugging since I can put it on a scope without taking anything apart.
The outlet isn't usable like this, but that's unlikely to be an issue any time soon since there are two of them. Once I'm sure that I'm happy with the software, I can just push the connector up into the cavity and then the outlet will be usable again. Here's a test after everything was installed onto the plastic pod:
After I got to this point, I went back to the car and spent a whole bunch of time trying to get the plastic handle things open so I could install the two parts of the beam sensor. I didn't make much progress, and decided that it was silly to waste any more time on it when I could just change the sensor from beam break to proximity. Beam break would have given more reliable signals, but changing to proximity allows me to install all components onto a single piece of the dash, not run any wires, and also hides the sensor components from view.
The change to proximity is almost as simple as inverting the logic in the software: turn the lights on when the IR beam is detected instead of when it goes away. In reality I also had to make some tweaks to increase sensitivity and chose a different phototransistor that performed better in that arrangement. You can see both versions of the software at the bottom of the post. After those changes, I drilled two small holes in the bottom of the plastic piece and stuck the IR sensor and emitter down there. The great thing about this location is that it's pretty much impossible to get your head low enough in the vehicle to see the bottom of this piece, so none of the modifications will be visible.
Here's a final test of the electronics before being installed in the car:
Installation in the car was very easy, just pop the pod back in and plug in the connectors. Here's a camera shot from below where you can see the mods, but you can't see these while you're sitting in the car.
And from the video at the top, you can see it works very well. So far it's properly detected my hand every time I reach into the tray, and I'll be watching to make sure I never get any false detects while I'm driving which would necessitate a code tweak.
Bonus project:
While I had the climate control piece out, I decided to swap some LED colors just for fun. I changed the passenger airbag indicator from orange to blue (this one always bugged me because most of the other indicators are blue), and I changed the seat heat indicators from both orange to orange and red to indicate low and high heat levels.